Pawtucket Tunnel project
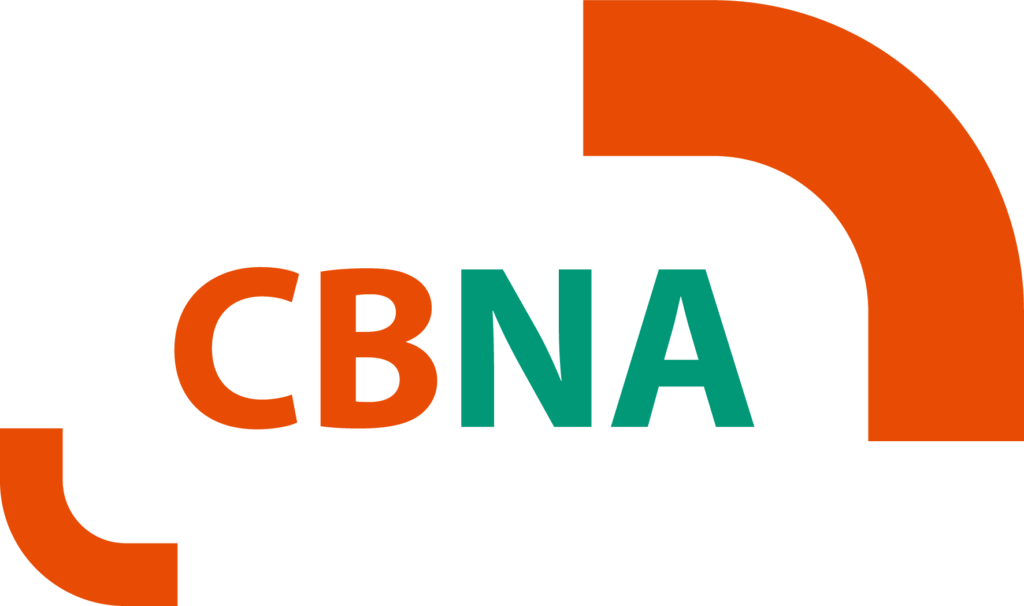
the project
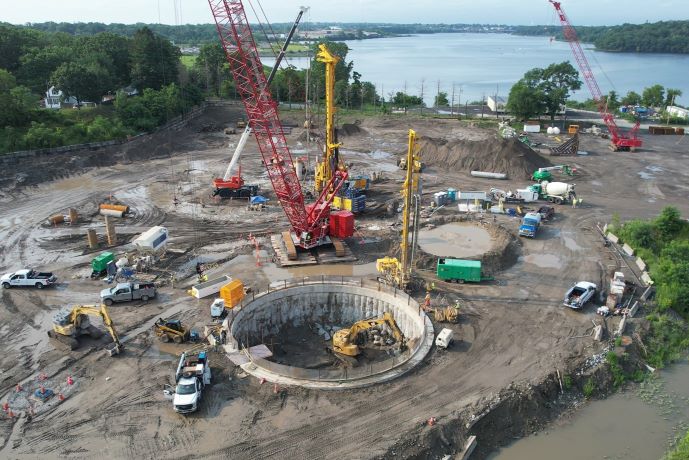
summary
Contractor: CB3A consortium (CBNA, Barletta Heavy Division and AECOM)
CB3A contract: $479.4 million
image: Narraganssett Bay Commission
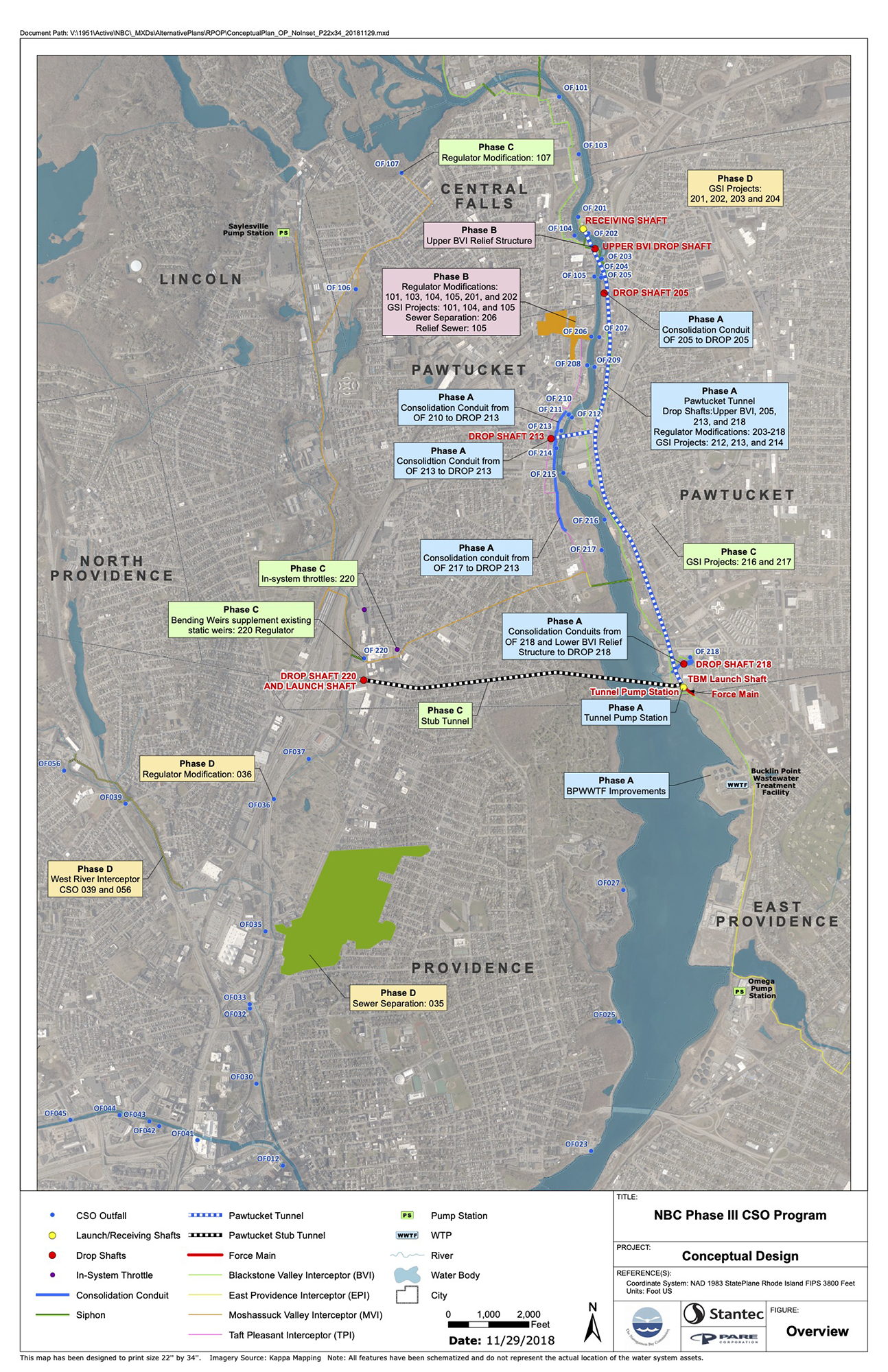
site overview
Narragansett Bay is a large natural harbour in Rhode Island, and New England’s largest estuary. The Narragansett Bay Commission, a non-profit public corporation, was created in 1980 and tasked with improving the water quality of the bay and its tributaries.
The “big dig” is the nickname for the Narragansett Bay Commission’s $1.5 billion CSO programme. Creation of the new Pawtucket Tunnel is the third and final phase of the big dig. A tunnel boring machine is being used to create a 2.2-mile tunnel alongside the Seekonk River. This tunnel will combine wastewater and potential flood water, and carry it safely to the Bucklin Point Wastewater Treatment Facility.
CB3A consortium turned to UBY to supply the sound and vibration monitoring solution required throughout the 4-year tunnel construction programme, as well as to provide software to manage communication with residents.
Image: CBNA
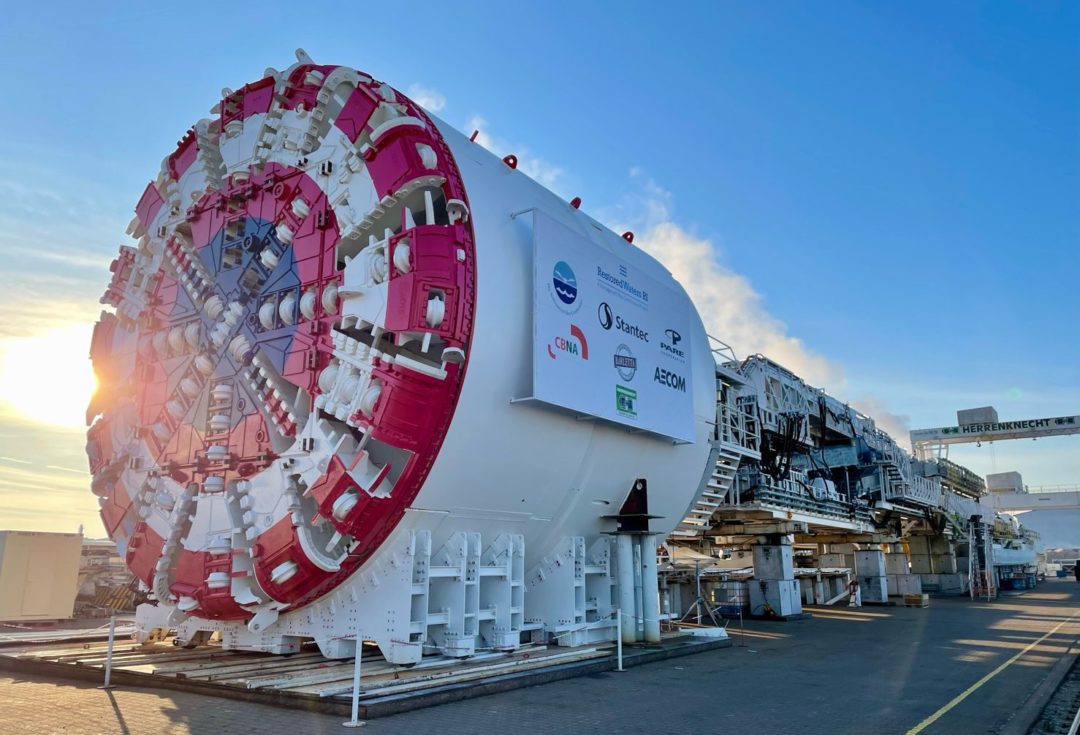
the challenge
Tunnel boring operations are inherently noisy, and the bay is the site of the state’s capital, Providence, among other communities, so careful monitoring of both noise and vibration is needed throughout the project.
The potentially affected area includes schools and hospitals as well as housing, and the consortium needed a solution that would enable managers to monitor noise and vibration without any continuous need to check in to a software platform, and which would help them resolve any threshold breeches or resident complaints as quickly and efficiently as possible.
UBY Solution
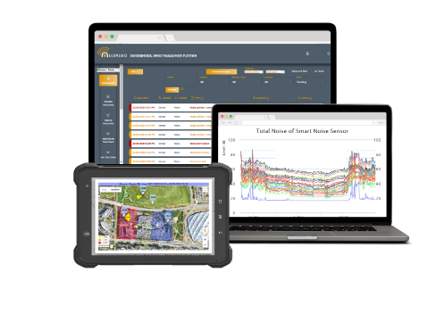
If such an issue did arise, the system went well beyond a traditional decibel reading. UBY’s own AI algorithms, embedded in the smart sensors, are capable of identifying the source of the sound, differentiating between jackhammers, traffic and other numerous noise categories, also allowing users to see visually the location of the source.
After receiving one particular noise complaint, the site supervisor was able to access the dashboard and immediately identify the cause (the ventilation system, with noise the result of human error in the launch shaft area) and act without any delay or further, potentially time-consuming investigation.
To find out more about UBY Environment
Benefits for the worksite
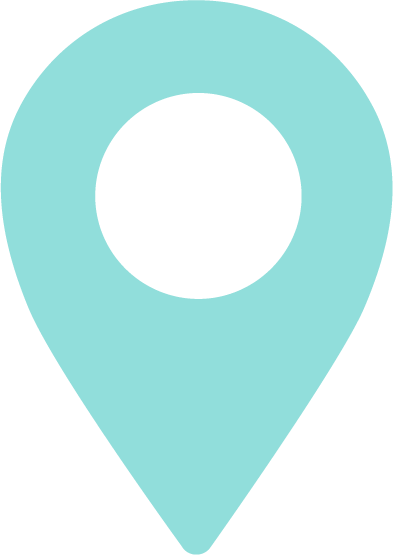
For project managers
When asked about the system, project managers highlighted the value of the automatically generated and customised weekly reports, which traditionally they would have needed to create manually.
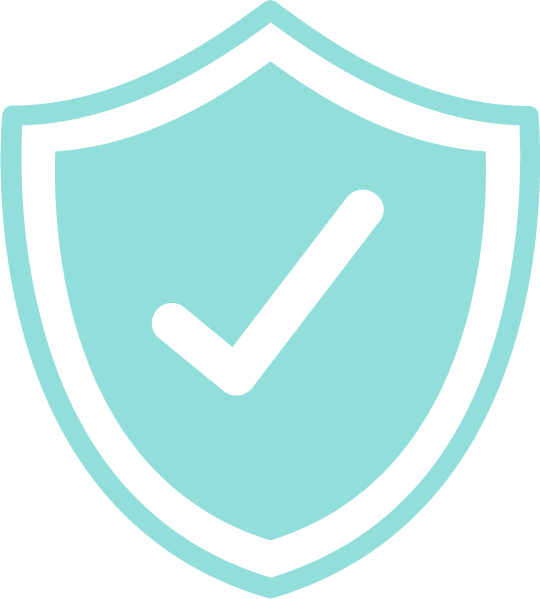
For local residents
Overall, UBY’s solutions resulted in a better experience for residents, accomplished with much less investment of managerial time for the contractor than would be required with traditional solutions.
Other UBY Environment references
- UBY Environment
- UBY Environment
- UBY Environment
Noise monitoring on an urban renovation project The Project Need to monitor noise disturbance caused by a general contractor during ...
- UBY Environment
- UBY Environment