Tracking small site equipment for a drinking water and wastewater pipe fitter
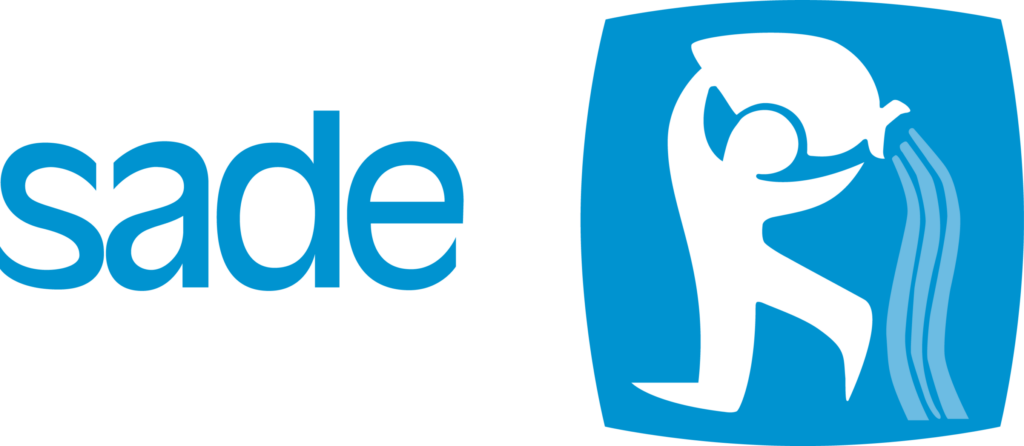
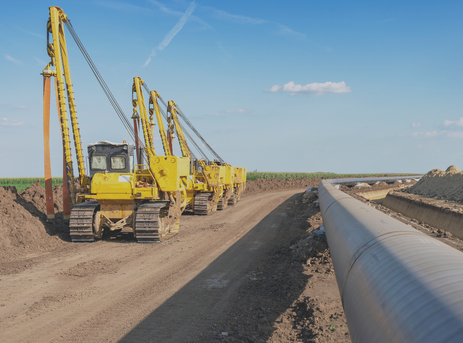
project
The Western Regional Division of SADE, a company specialising in the design, construction, rehabilitation and maintenance of networks and infrastructures, has called on our connected fleet management solution to optimise the monitoring of its fleet of small items of equipment.
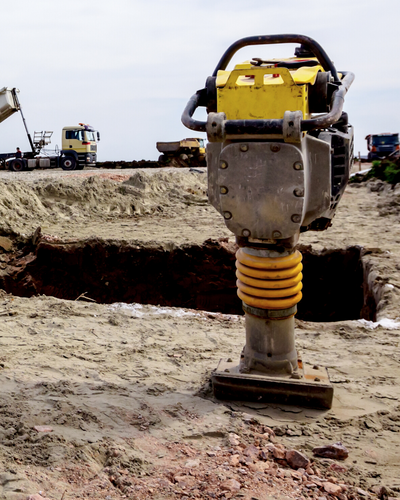
challenge
One of the major issues facing Sade’s Western Regional Division was how to manage this type of equipment. When the management of all the equipment pool was set up at regional level, the information (volume, condition, location, etc.) relating to the small equipment pool was incomplete. Identifying the equipment available and its level of compliance was difficult to obtain centrally.
The challenge then lay in our ability to provide them with factual, rather than declarative, data on:
- the availability and location of the equipment,
- the level of compliance,
- equipment usage,
- dormant stock in depots.
They also want to manage assignments by associating equipment with a person or a team (or agency).
Project start: 2021
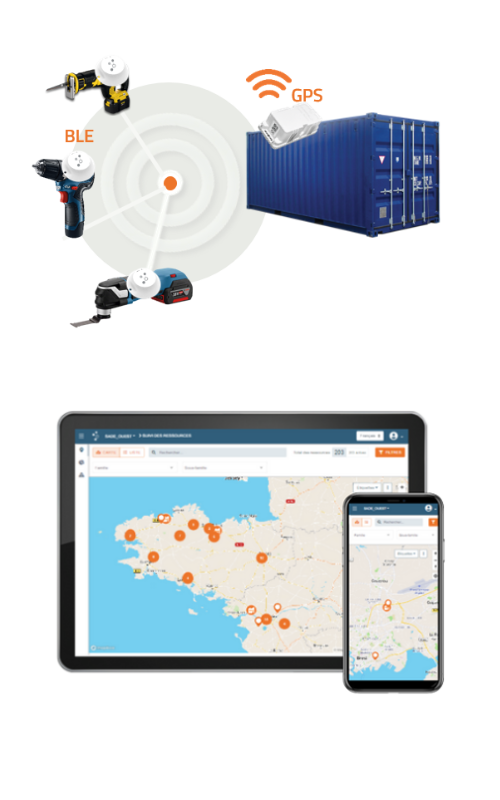
uby solution
Geolocation system deployed on equipment
More than 200 items of equipment have been connected in order to monitor their deployment in the region’s branches.
Equipment location, automated container inventory and regulatory control monitoring
Using the equipment fleet management application, the equipment team at the Western Regional Division can locate the various items of equipment on a map and obtain the position of their containers as well as the list of equipment available in each container.
Our application also enables them to manage the regulatory inspections of their equipment fleet by providing access to the list of equipment to be inspected and its status.
Benefits for the operation
Savings on two levels
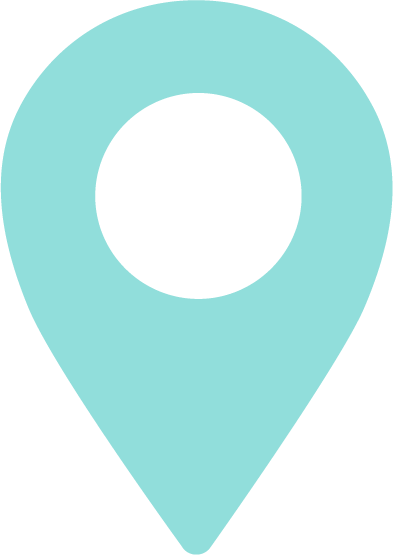
Avoid over-investment
By locating equipment, the equipment team can easily detect dormant equipment, thereby improving its utilisation rate.
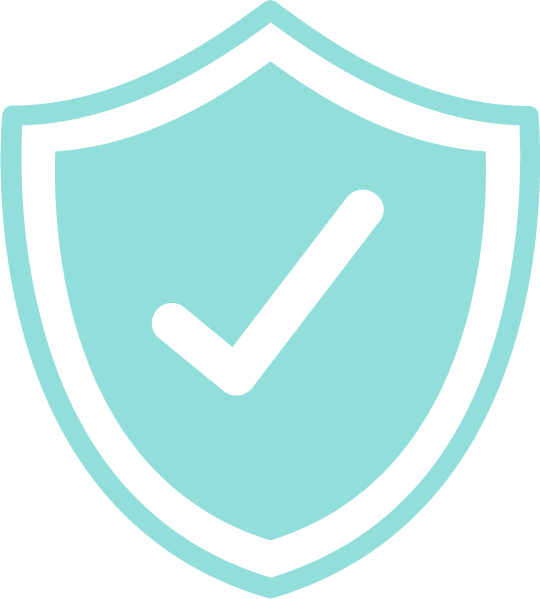
Maintain equipment in operational state
By keeping up to date with statutory inspections and optimising the use of equipment, the lifespan of equipment can be extended.
By monitoring their fleet of small items of equipment, Sade’s regional management has adopted a CSR approach. Thanks to the activity data collected on the equipment, the Equipment team can now apply reasoned purchasing. In addition, maintenance is carried out at the right time, which increases the life cycle of the equipment.
Our UBY Productivity references
- UBY Productivity
- UBY Productivity
- UBY Productivity