Why efficiency and productivity are key to the future of Australian construction
With a boom in infrastructure projects and a national conversation about government plans for new housing and the need to upgrade public buildings, attention is on the construction industry and how it will need to scale rapidly. Already, demand for construction services in Australia is high and expected to grow, with significant government investment – in particular projects in education, transport, power and energy, and utilities. The Australian construction industry is also facing challenges, including rising costs, labour shortages, and high-profile delays to public projects. But, looking ahead…
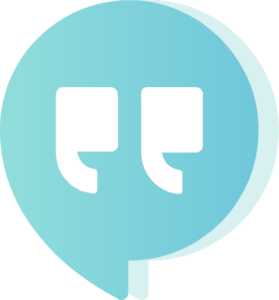
“In Australia, the engineering and construction industry outlook is positive. Those that can successfully navigate through the short-term challenges should be able to capitalise on the huge pipeline of opportunities that lie ahead.”
This is KPMG’s assessment in its latest Global Construction Survey, adding:
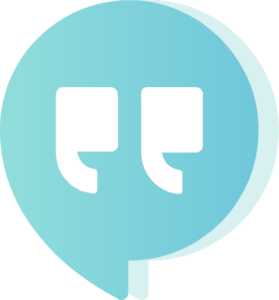
“Companies need to continue to develop new and innovative ways to improve productivity and project performance.”
There is huge potential for growth in the Australian construction sector, and rapid adoption of new technology will be key to overcoming challenges and delivering the improved productivity necessary for success.
Help teams work safely and efficiently
The construction industry will need nearly half a million additional workers by 2026 to meet demand and replace retirees. One of the challenges of ongoing labour shortages is the need for teams to work more effectively while maintaining the highest standards of safety. Labour costs are also increasing so, to meet budget demands, improving productivity and preventing project overruns is key.

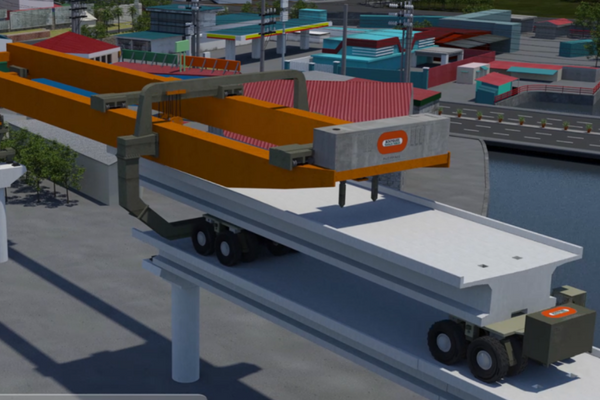
There is real potential for change in construction productivity, and technology is driving that
Worksite insights have never been more critical – and understanding how your project is progressing in real-time can help you minimise unexpected costs, stay on schedule, and anticipate risks. UBY offers smart AI-powered monitoring solutions that support construction project managers – making projects more efficient and productive.
Looking for support on your next project? Contact us by email ausenquiries@uby-group.com or via the website